The typical manufacturing company will break its inventory down into three categories: raw materials, work-in-process, and finished goods. This helps to ensure that the manufacturer is maximizing production and storage space. It also helps to identify the cost of each item used in the creation of a product. Using this method, the manufacturer can calculate the total costs of the product, which is then used to determine the cost of goods sold.
Raw materials include basic inputs of production such as wood, plastic, and metals. Materials that are not directly used in the production process such as lubricants, cleaning supplies, and disposable tools are considered indirect raw materials. A small amount of indirect raw materials can be reported as an expense, but they are usually accounted for under manufacturing overhead.
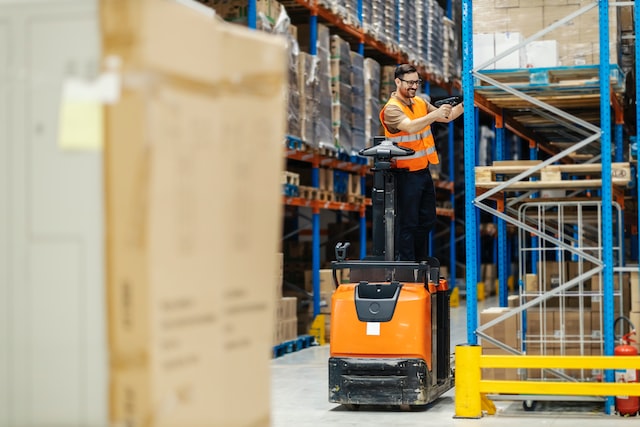
Work-in-process inventory (WIP) represents the stage of the manufacturing process where items are still being produced. The value of this inventory includes direct labor costs, indirect manufacturing costs, and the direct costs of material. An example would be a jam that has not yet been labeled, but is still cooking. However, this type of inventory is not always fully converted to finished goods.
Finished goods represent the goods that are fully manufactured and ready for sale. These products are often in sellable condition and labeled. In some cases, these products can be sold exactly as they were purchased. Another example of finished goods is a home built by a home builder. Other products, such as a shoemaker’s loafers, may be sold in modified form.
Manufacturers typically report a cost of goods sold on their balance sheets, which includes the value of direct and indirect raw materials. It can also include the cost of labor, factory utilities, and manager salaries. Companies are required to disclose any reserve for obsolete inventory on the balance sheet.
Likewise, companies that use patents in the manufacturing of their products must report the cost of these patents. These costs will also be recorded under the intangible assets section of the balance sheet. For instance, the capitalized costs associated with patents would be added to the intangible asset line in the balance sheet.
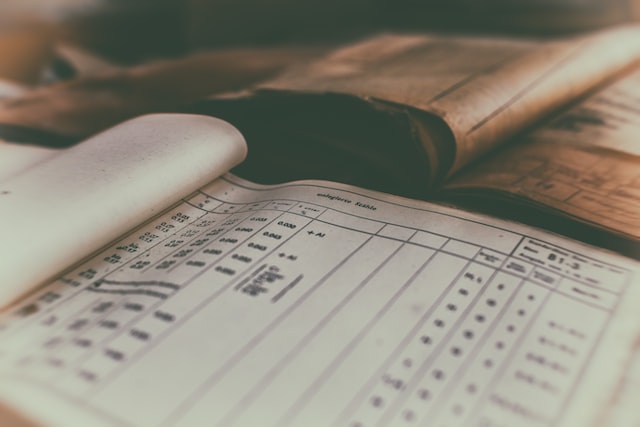
Manufacturers will then place their inventory on the balance sheet in the following order: cash, short-term investments, receivables, and current assets. They will then position the rest of the inventory, which is usually listed in notes to the financial statement.
Lastly, manufacturers will report the cost of their finished goods in the finished goods inventory line. This is similar to the other types of inventory, but it is only one piece of the overall inventory count. Although this is one of the smaller pieces, it is a useful tool for businesses that are uncertain about the demand for their products.
Finally, manufacturers should not overlook the importance of inventory turnover. Inventory turnover is a key factor in determining the sales frequency of a product. If a retailer is unable to purchase a particular product, it can cause the manufacturer to lose money.
Photo by Petrebels on Unsplash